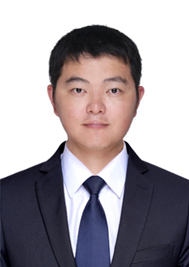
Leilei Ji
Doctor of Engineering
Associate Professor
TEL: +(86) 18806286122
Email: jileileidemail@163.com; leileiji@ujs.edu.cn
Location: Research Center of Fluid Machinery Engineering and Technology, Jiangsu University
Biography
Dr. Leilei Ji is an associate professor at National Research Center of Pumps, Jiangsu University, China. He obtained his PhD in Engineering in Fluid Machinery from Jiangsu University in 2021. He was a visiting scholar in Prof. Ramesh Agarwal’s group at Department of Mechanical Engineering & Materials Science, Washington University in St. Louis from 2019-2020. And, from July 2024, He is a sponsored researcher in Prof. Xuesong Wu’s group at Department of Mathematics, Faculty of Natural Sciences, Imperial College London. His research interest is focused on design and optimization of advanced devices for high-efficiency pumped storage and hydropower utilization. He has published more than 70 original papers, hold over 10 patents, and has authored two technical books.
Fields of research:
[1]Computational Fluid Dynamics (CFD)
[2]Tip leakage flow and its induced rotating stall characteristics
[3]Unsteady flow and its control technology of vane pump
[4]Transient process theory and characteristics of hydraulic machinery
[5]Internal flow mechanism and cavitation turbulence structure of waterjet propulsion pump
[6]Study on hydraulic performance optimization and rotor dynamic characteristics of vane pump
[7]Research on Engine Cooling Water Pump Performance Optimization and Cavitation Mechanism
Main Publications:
[1]Mixed-flow Pumps: Modeling, Simulation, and Measurements [M]. ASME-Wiley, 2024.(Book)
[2]Theory and characteristics of transient processes in mixed-flow pumps[M]. Jiangsu University Press, 2021.(Books in Chinese)
[3]Optimization of pump transient energy characteristics based on response surface optimization model and computational fluid dynamics[J]. Applied Energy, 2024, 362: 123038. (SCI&EI, Q1, IF: 11.2)
[4]Energy Characteristics of Mixed Flow Pump under Different Tip Clearances Based on Entropy Production Analysis[J]. Energy, 199 (2020) 117447. (SCI&EI, Q1, Highly Cited, IF: 8.795)
[5]Effect of blade thickness on rotating stall of mixed-flow pump using entropy generation analysis[J]. Energy, 2021, 236:121381. (SCI&EI, Q1, IF: 8.795)
[6]Diagnosis of internal energy characteristics of mixed-flow pump within stall region based on entropy production analysis model[J]. International Communications in Heat and Mass Transfer, 2020, 117: 104784. (SCI&EI, Q1,IF:3.971).
[7]Effect of circumferential spokes on the rotating stall flow field of mixed-flow pump[J]. Energy, 2024, 290: 130260. (SCI&EI, Q1, IF: 8.795)
[8]Energy dissipation mechanism of tip-leakage cavitation in mixed-flow pump blades[J]. Physics of Fluids, 2024, 36(1): 015115. (SCI&EI, Q1, IF: 3.971)
[9]Prediction model for energy conversion characteristics during transient processes in a mixed-flow pump[J]. Energy, 2023, 271: 127082. (SCI&EI, Q1, Highly Cited, IF: 8.795)
[10]Effect of circumferential spokes on the rotating stall flow field of mixed-flow pump[J]. Energy, 2024, 290: 130260. (SCI&EI, Q1, IF: 8.795)
[11]Study on the trajectory of tip leakage vortex and energy characteristics of mixed-flow pump under cavitation conditions[J]. Ocean Engineering, 2023, 267: 113225. (SCI&EI, Q1, IF: 5)